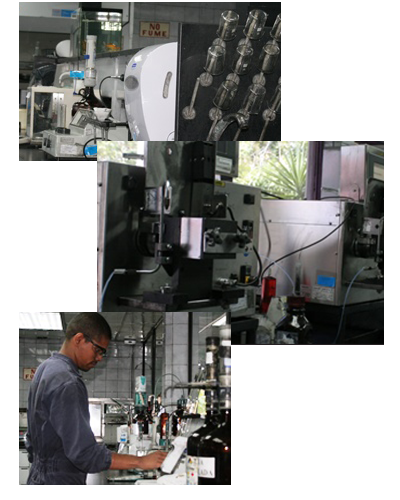
En Negroven
Los atributos físicos y químicos (tamaño de partícula, área superficial, estructura, actividad superficial) del negro de humo, pueden cambiar las propiedades del elastómero en diferentes formas y diferentes grados. La carga de negro de humo es un factor crítico para alcanzar el grado de modificación deseado del elastómero con lo cual impartirá al compuesto de caucho propiedades adecuadas para una aplicación determinada.
Un mezclador de caucho (rubber compounder), debe saber seleccionar el polímero, el negro de humo y la combinación de carga correctos y el sistema de vulcanización adecuado, para lograr un compuesto de caucho al menor costo posible.
Área Superficial: El área superficial de un negro de humo es muy importante porque define cuánta superficie está disponible para interactuar con otros materiales presentes en un compuesto de caucho. Los negros de pequeño tamaño de partícula, generalmente tienen una alta área superficial. El tamaño de la partícula ejerce una gran influencia en las propiedades cromáticas. Las partículas de menor tamaño tienen colores más intensos y mayor viscosidad y requieren más energía para la dispersión.
Estructura: La estructura primaria es usada para describir el grado en el cual las partículas de negro de humo están unidas en agregados. La estructura secundaria es la aglomeración de los agregados, debido a las fuerzas de Van der Waals y son formados durante la peletización del negro de humo. La agregación contribuye en casi todos los efectos relacionados a la estructura, observados en los compuestos de caucho, mientras que la aglomeración es fácilmente destruida durante el mezclado del caucho y tiene menor efecto sobre las propiedades de los compuestos de caucho. Negros de Humo con una alta estructura proporcionan mayor viscosidad y fácil dispersión.
Propiedades Químicas y Actividad Superficial: La naturaleza química de la superficie de un negro de humo es variable. Hay evidencia de la presencia sobre la superficie de al menos cuatro grupos que contienen oxígeno: Carboxyl, Phenol, Quinona y Lactona. Las superficies también pueden diferir en capacidad adsortiva y en la distribución de los sitios de alta energía. Los negros de humo con superficies químicamente modificadas no han demostrado ninguna mejora notable en refuerzo en compuestos de caucho. Los grupos de superficies químicas afectan la velocidad de curado con muchos sistemas de vulcanización. No hay un procedimiento estándar para la estimación cuantitativa de la superficie química y la actividad superficial del negro de humo. Sin embargo, una medición relativa de la oxidación de la superficie se puede obtener a partir de la medición del pH y la pérdida de peso al secar el negro de humo a 950°C.
Conductividad Eléctrica y Térmica: Los negros de Humo son generalmente eléctricamente conductivos debido al esquema de fuertes enlaces presentes en las regiones cristalinas. Incrementando la estructura y el área superficial, ambos contribuyen a incrementar la conductividad eléctrica.
En conductividad térmica, los efectos del elastómero eclipsan los efectos del negro de humo. Especialmente los negros para alta conductividad eléctrica son generalmente altos en estructura y pueden ser porosos. Estos negros no necesariamente dan la mayor conductividad térmica, probablemente debido a su naturaleza porosa que provee un alto aislamiento.
Calidad del Pellet: El necesario peletizar el producto por razones económicas durante el transporte del material y para mantener un flujo adecuado del producto en contenedores de transporte a granel y equipos de transporte en general. Estos pellets deben tener suficiente dureza para resistir el esfuerzo físico durante el transporte y el manejo del material en la planta, pero ser suficientemente blandos para romperse y dispersarse durante el proceso de mezclado con el caucho.
Los requerimientos de Dureza de Pellet dependen de la naturaleza del compuesto en el cual va a ser utilizado el negro de humo. Los compuestos que usan polímeros de baja viscosidad, usualmente requieren pellets suaves.
El porcentaje de Finos y Atrición es considerado como un indicador de las características para el manejo de producto a granel y de las facilidades durante el mezclado con el caucho.
La Resistencia de Masa refleja la fluidez del negro de humo en los despachos a granel.
La Distribución del Tamaño de Pellet algunas veces es importante. Generalmente no es conveniente tener altas concentraciones de pellets grandes debido a su tendencia a fragmentarse más que a desmoronarse y por tanto, a no facilitar la dispersión.
Pureza: La pureza del negro de humo generalmente se juzga a partir de las pruebas de decoloración con tolueno, ceniza, residuo de grit y el contenido de azufre.
La Decoloración con Tolueno da una estimación aproximada de la cantidad de material extraíble presente o materia prima (Hidrocarburo) que no se convirtió en carbón.
La Ceniza surge principalmente a partir de las sales del agua utilizada en la sofocación de la reacción y en el agua de la peletización, con alguna contribución de impurezas de materiales que no son hidrocarburos en la materia prima.
El Grit o el Residuo al Tamiz es material suficientemente grande para quedar retenido en las mallas 35 o 325 del tamiz. Las fuentes principales del grit son coque, formado en el reactor, refractario erosionado de las paredes del reactor y metal de los equipos del proceso.
El Azufre en los negros de humo de horno, proviene de la materia prima y varía de acuerdo con el contenido de azufre en el hidrocarburo. La mayor parte del azufre está químicamente unido y parece estar distribuido por todo el agregado de negro de humo. Los negros de humo con niveles de azufre hasta de 1.5% no parecen influir en las velocidades de curado.
El Oxígeno presente está químicamente combinado sobre la superficie del negro de humo, mientras que el Hidrógeno está distribuido en toda la partícula.
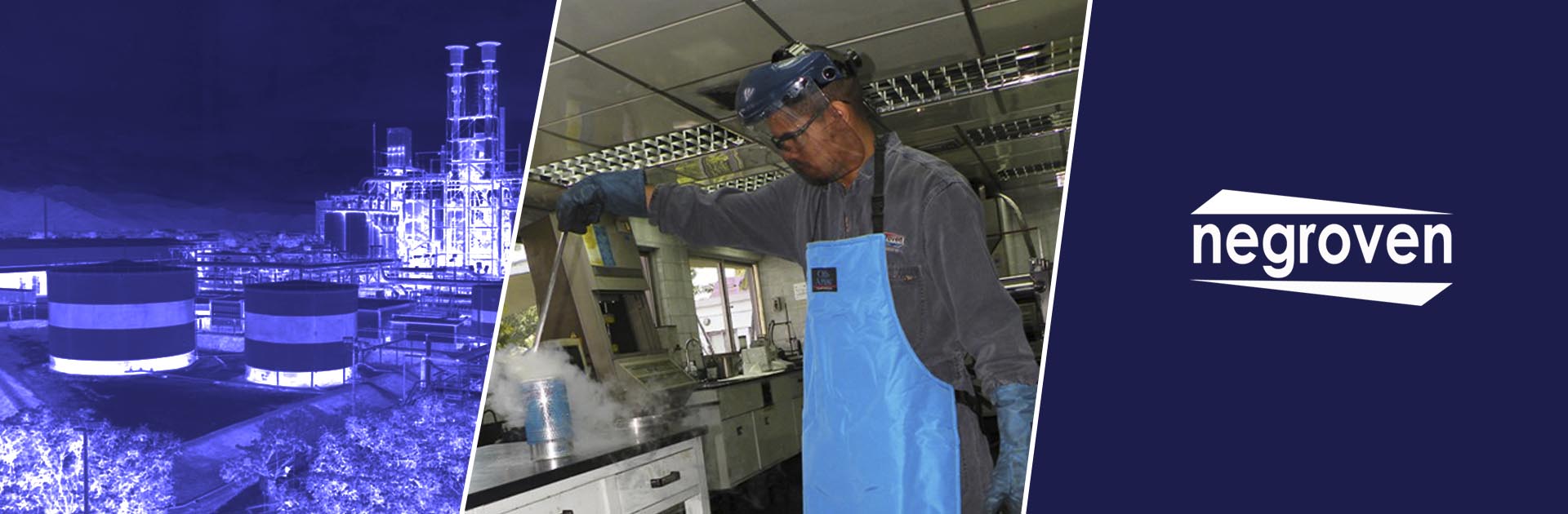
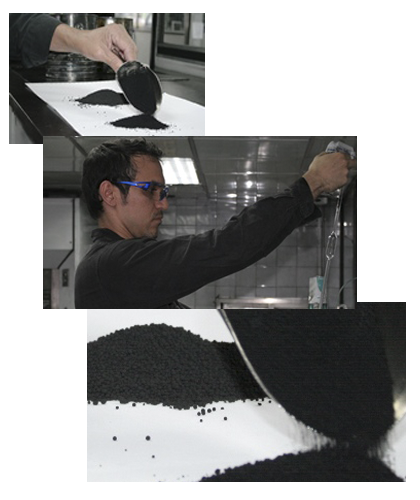
El Negro de Humo es carbono químicamente puro.
Se produce en reactores especialmente diseñados, mediante la descomposición térmica de un hidrocarburo utilizado como materia prima.
Las altas temperaturas imperantes en el reactor provocan la ruptura de las moléculas del hidrocarburo en sus dos componentes básicos: carbono e hidrógeno. El carbono es el Negro de Humo que así obtenido, conjuntamente con los gases de combustión, avanza a la etapa de filtrado, donde el negro de humo es separado de los gases.
A continuación, el Negro de Humo en polvo que proviene de la fase de filtrado, pasa a la fase donde se densifica mediante una peletización y posteriormente se conduce a la fase de secado donde adquiere las condiciones finales del producto.
Finalmente se envía a los silos de almacenamiento, desde donde se alimentan los sistemas de ensacado y llenado a granel.
Todo el proceso, desde la recepción de la materia prima hasta el despacho del producto terminado, es monitoreado y el producto analizado y controlado bajo estrictas medidas, con la finalidad de garantizar su calidad a los clientes.
A escala mundial, los productos de caucho consumen el 90% del Negro de Humo producido, donde es empleado para imprimirle características de refuerzo, resistencia al desgaste, resistencia al rasgado, facilidad de extrusión, entre otras características, constituyendo una parte importante en peso de los productos de caucho.
El 10% restante de la producción mundial de esta versátil materia prima encuentra aplicación en tintas para periódico, tintas para impresoras, tintas para bolígrafos, pinturas, papel carbón, plásticos, empaque para alimentos, delineadores de ojos, así como muchos otros artículos para uso industrial, doméstico e inclusive de cuidado personal y belleza, para los cuales, en muchos casos, se utilizan distintos Negros de Humo especiales para lograr características específicas requeridas por cada artículo.